Despite 94% of supply chain managers claiming that digital transformation will fundamentally change supply chains in 2018, only 44% have a strategy ready. Have you?
The digital retail industry
The retail industry as a whole is becoming more digitised. Online shopping is now the norm, consumers can buy items straight from social media platforms and contactless and mobile payments are being offered in-store. And the digital revolution isn’t leaving the supply chain behind.
Increasingly complex supply chains with hundreds or thousands of suppliers are difficult to track (especially without a platform to help you do so) but it’s an issue that needs to be addressed in 2018. Supply chain has been predicted to be the biggest retail disruptor right now – with the ability to master the modern supply chain (or not) being the largest difference between those who fail and those who don’t.
Supply Chain Technologies
In recent years, more companies have been using supply chain technologies to manage their complex internal processes, with the most popular solution being product lifecycle management (PLM), enterprise resource planning (ERP) and radio-frequency identification (RFID). Using technology vastly reduces the risk of human error.
PLM systems offer a new level of control and visibility over production processes. By collating data relevant to a product’s complete lifecycle, PLM can produce a blueprint with all inputs, outputs and processes clearly defined. Gartner states: “As part of the strategy that apparel companies have pursued to use IT to scale efficiencies, enable innovation and make consumer-centricity possible, PLM can play a crucial role in creating fresh and innovative products and delivering them to market in a timely and profitable manner.”
ERP has been referred to as “the heart, brain, and backbone of a company” due to its ability to handle huge amounts of information needed to run a modern multichannel retail business. This solution makes tracking products to market and activity handling smoother and easier.
Without a doubt, ERP and PLM systems have improved visibility into supplier compliance but they’re still a far cry from providing a fully ethical and transparent supply chain.
Using digitisation to create an ethical supply chain
Like any large task, tracking your entire supply chain is easier if you know where to begin. Start with supplier management. Which suppliers do you deal with directly? The companies who provide you with your completed products are your Tier 1 suppliers. Then find out who supplies them – these are your Tier 2 suppliers. The factories supplying your Tier 2s are your third-tier suppliers and so on. With the right software, you can continue this process all the way down to raw materials.
One question we often get asked at Segura is “how do I know my Tier 1s are really ordering from my Tier 2s and not from somewhere else?” We can help with that. The Segura platform provides full downstream visibility of all orders in their supply chain, allowing the brand or retailer to see each order that has been place. For example, you can see when the care labels for your garments are ordered and who received the order. If a purchase order doesn’t show on the system, it hasn’t been placed through Segura. It’s that simple.
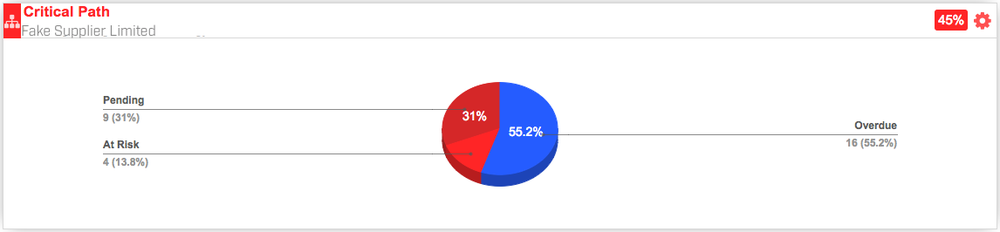
Although this is only a snippet of what Segura can do, through this process you can guarantee where every component has come from, every time.