In September 2016, BBC Panorama uncovered Syrian refugees working in the supply chains of major retailers. In their report, Panorama investigated multiple factories and found both adult and child refugees working illegally to make clothes to be sold by retailers in the UK.
It was confirmed by one fashion retailer that, despite their clothes being made in one of the implicated factories, they had not approved that supplier to produce for them. This poses the question: how can a retailer be using a supplier, without them being aware of it?
Nominated Supplier Policies
Despite many retailers having existing nominated supplier policies in place, manufacturers often source product components from unauthorised/unknown suppliers, potentially severely impacting on the quality of the retailer’s product. Retailers therefore have very limited visibility and control beyond their primary suppliers.
The first step to fixing this problem is implementing a policy whereby all components must be ordered through approved suppliers. Implementing a policy is unlikely to be sufficient, as proven in the BBC Panorama report. Implementing closed-loop order tracking means that retailers not only have visibility of the orders within their supply chain, they can also track them. Segura can help. The Segura platform works as a hub, through which all orders must be placed, regardless of its position in the supply chain. This allows the retailer to have full visibility of their entire supply chain.
For one retailer, the use of Segura uncovered that 80% of their components were being sourced from unapproved suppliers.
Solving the Problem
The existence of many different quality approval systems throughout a supply chain can make it difficult to track orders, as they are often placed before all necessary approvals are made. A quality gated order process can be implemented alongside an organisation’s order management system to compile all quality approval processes from across the supply chain. Segura software allows retailers and suppliers to view pending orders in real time. Furthermore, this visibility allows the retailer to gather data surrounding recurring quality problems and find common points of failure.
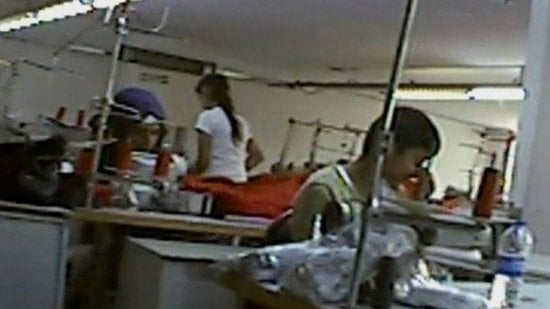
Currently, when a quality problem occurs, it can be difficult to trace the source of the garment’s components and find the root cause of the problem. Through the use of unique garment tagging and RFID tags, retailers are able to trace garment components back to the source, allowing the implementation of a root cause analysis process.
One major retailer told Panorama that through their own inspections, they had been unable to locate any Syrian refugees working within their supply chain. This raises the question: are audits really enough? A refugee described how they are removed from the factory when an audit takes place, to prevent their detection. Segura software can map audit certificates, as well as their expiry dates, from multiple sources. This can alert the retailer to any issue that may not have been found in their own audit, but may have been uncovered by another source.
Despite the severity of the issues raised by BBC Panorama, through a bite-sized, step by step approach, any retailer will be able to overcome these problems, and in turn increase their own profitability.
All retailers could benefit from increased supply chain visibility, improved quality and greater compliance, (oh, and increased profits too….)
Originally Published 12/09/2017