Supply chain mapping gives you visibility of your supplier network, helps mitigate risks and enables you to achieve compliance with confidence.
Retailers in the fashion and apparell industry have complex global supply chains spanning multiple tiers and continents. This complexity creates a significant challenge when striving for supply chain transparency, ethical sourcing, and compliance with emerging legislation.
What is supply chain mapping?
Supply chain mapping is the process of capturing the stages and flow of goods, services, and data throughout the multiple tiers of your supply chain. A product supply chain map should capture data from: suppliers, manufacturers, distributors and vendors, and include the connections between them.
All businesses looking to mitigate risk, reach strategic ESG goals, strengthen supplier networks and make cost savings, accurate supply chain mapping and transparency are essential.
Is your supply chain mapping process up to scratch?
- Is your published tier-1 supplier list up-to-date?
- Have you mapped all your tier-2 suppliers?
- Have you mapped your suppliers beyond tier-2, in order to check on ethical standards, calculate material composition, or to validate green claims?
- Do you have a single source of supplier data across all your departments?
- Do you have an 'active supplier list' that updates automatically as new suppliers are onboarded?
- Can you easily run reports on your supplier data, as required by different business departments, knowing that your data set is accurate and up-to-date?
Answer no to any of these questions? Then this guide is for you. It provides a clear methodology for the process of mapping your entire supply chain, from tier-1 suppliers to the origins of raw materials.
What is the purpose of supply chain mapping?
Supply chain mapping creates a centralised database for all of your supply chain data, allowing you to report on and segment your data with ease. It offers businesses enhanced supplier visibility, allowing them to identify potential risks or vulnerabilities.
Supply chain mapping is an essential step to reaching supply chain transparency, and this in turn enables retailers and brands to meet new and upcoming global legislative requirements.
What supply chain data should be captured?
Engaging with your suppliers to map your supply chain will capture a wide range of data, including, but not limited to:
- An inventory of all known/active suppliers, their offices and their factory sites
- Details of any subcontractors or agents and their relationships with your suppliers
- Details of the products or services that each supplier provides
- Confirmation of component sourcing as you move through the tiers
- All data that passes between your company and suppliers (and its importance/value)
- Evidence of any required certifications and audits (including Corrective Action Plans (CAPs)), as well as deadlines and renewal dates
- Any agreements, T&Cs or contracts held with suppliers including renewal dates
Segura is a supply chain mapping tool, designed to keep your business's supply chain data is always accurate and up-to-date by:
- Monitoring and reconciling supply chain information
- Allowing suppliers to directly update their data
- Identifying potential risks with suppliers, contractors and their subcontractors
- Creating a visual representation of your supply chain map that is easy to interact with and report on
The benefits of mapping a supply chain and gaining transparency
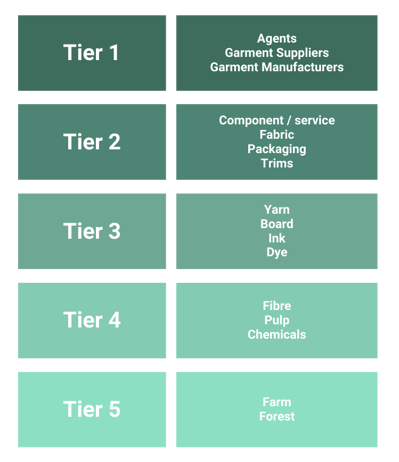
- missing nominated supplier audits,
- failing to ensure safe working conditions,
- failing to expose and prevent forced or child labour, or
- causing irreversible environmental damage
If consumers perceive a retailer has been neglectful, resulting in a negative event, the consumer will hold the retailer ultimately responsible, as the video below illustrates.
In the process of mapping the supply chain, the retailer aims not only to identify all suppliers and their roles but also to address legislative obligations, conduct risk assessments, and fulfill their ESG commitments.
Another benefit of mapping the supply chain is gaining insights into how suppliers interact and overlap, which can lead to greater efficiency and reduced waste. Achieving all this through Excel spreadsheets is time-consuming and challenging, which is why Segura, a powerful supply chain mapping tool, is an ideal solution for the task.
6 Steps to the supply chain mapping process
It’s clear that supply chain mapping empowers businesses in several ways, but what should the supply chain mapping process look like?
The Segura system is effective because it uses an order-level 'chain of custody': suppliers must use the supply chain mapping software in order to accept a purchase order. Thus suppliers are heavily incentivised to get on board! Adding suppliers can be done gradually through a supportive process including supplier training, and by inviting them in manageable groups, by size, location, material or service provided etc.
Step 1 - Identify and onboard known suppliers
Your tier-1 suppliers are those you or your agents work with directly. They are (usually) used to being asked for information, are supportive and able to help address any gaps in your data.
Through Segura, you can invite suppliers to register on the platform, prompting them to fill in key information confirming their identity, their location and what they do. Where you have already manually captured this information, Segura can import it and ask suppliers to verify what’s there as well as supply any missing details. This radically speeds up the process of capturing the right data.
If a supplier is involved in the production, storage, or distribution of your products, they should be on your supply chain map, even if you don’t work with them directly.
Step 2 - Onboard and start to map your upstream suppliers
Once your tier-1 suppliers have completed their registration and provided all the necessary information, you can gain valuable additional data, and enable them to seamlessly accept your purchase orders through Segura, so you will always know your active tier-1 suppliers.
However, this is just the beginning. Your tier-1 suppliers will also be asked to disclose their own suppliers and subcontractors who provide the components and services used in your products.
We reviewed a few other systems similar to Segura but none really met our criteria. Segura's platform had the missing link we needed, which was the fact it linked to the purchase order. Segura provided us with a real-time chain of custody by order, down to tier 4 and beyond. It was simple for both River and our suppliers to use, and it quickly gave us the reporting we needed to meet our pledge of transparency. Unlike other companies, Segura understood our needs and were very easy to work with. We quickly realised that Segura and their platform was the one for us.
Ethical Trade Manager, River Island
When your tier-1 suppliers declare their suppliers, you will start to uncover and capture your products' bill of materials. This enables you to invite upstream suppliers to register on Segura and confirm they have provided the components or services to the tier-1 suppliers. This process ensures supply chain traceability, which is invaluable when ensuring compliance with legislation.
You are then able to cascade this process through your entire supply chain, according to your priorities and schedule.
Step 3 – Strengthen supplier relationships
Supply chain mapping helps to strengthen relationships with your suppliers. It improves communication and reduces duplication of data-sharing and manual data-capture via email.
Suppliers can go to Segura and complete all data required for your business. It provides all suppliers with a clear understanding of, not only your business needs, but also one another’s needs, expectations and goals at every tier.
Another unexpected benefit is that where there is overlap, and different retailers use the same suppliers, those suppliers are already familiar with the Segura system. We are also advocating for shared data collection points for compliance to help suppliers reduce the work they have to meet multiple and varying requests for data from their customers.
As we gain more transparency in our supply chain, we are also growing stronger partnerships with our suppliers
Step 4 - Identify risks and benefits
Gaining a deeper understanding of your multi-tier supply chain, including suppliers, contractors and relationships, makes it easier to identify potential risks and mitigate their impact on your business.
Supply chain mapping allows businesses to identify where value can also be added (e.g. more sustainably sourced components and/or raw materials). Simultaneously, mapping the supply chain helps identify areas where value could be lost such as through quality control issues or disruptions from natural disasters that delay production or delivery.
Having a platform like Segura will help with uncovering the materials and components for our products, coupled with where they come from, in much greater detail. Supply chains have become more dispersed and global, and in turn, so have data capture and reporting. Segura will provide us with access to real-time, accurate information. Segura’s ability to capture and enable us to monitor our emissions and ESG standards is vitally important to our business and goals
Assistant QC Manager at Schuh
Supply chain mapping empowers businesses to identify opportunities to make their supply chain greener, more ethical and more sustainable. Indeed it helps with anything from capturing relevant data to monitor and reduce emissions or water consumption, to performance managing suppliers with a poor ethical or ecological track record. This can only have a positive impact on your ethical and sustainability credentials.
Step 5 – Import additional data
Segura allows you to easily import data from external sources, enabling you to combine information and report at a wider scale. This can prove invaluable when identifying additional areas of cost-saving, efficiency improvements or potential vulnerabilities within your supply chain. For example you may want to import data from the Higgs Index, or you may want to sync with your Product Lifecycle Management (PLM) system.
Step 6 - Maintaining and monitoring the data
Once your data is captured, reported, and reviewed, Segura automates the maintenance process. Suppliers are automatically notified when certificates, audits, or agreements require updates, allowing them to make changes directly. This reduces the manual admin burden on your staff, allowing them to focus on driving improvements and removing risks.
Our supply chain is complex and, with consumers demanding increased transparency from all businesses, we’re proud to be reaching this milestone with Segura. Investing in the right sustainability tools is essential to driving towards our 100-1-0 goals. The Segura platform not only meets our needs today but also has the flexibility to help us build transparency and traceability into our business for the long term.
Positive Business Director at Pentland Brands
General advice when mapping the supply chain
Avoid departmental silos
Involve all key teams. Buying, CSR/Ethical and Sustainability, Finance teams can better align and work together. When mapping the supply chain through Segura, one of the benefits is increased supplier visibility within your internal teams, ensuring that each team member is reviewing the same centralised data.
This increases cross-departmental collaboration, reduces business risk and increases efficiency.
Not only does each brand have full sight of their supply chain and the information relating to each supplier, helping us to achieve our strategic goals, but with all UK Brands utilising the same platform it will allow us to view all supply information in one place, which will be very powerful.
Head of CSR and Sustainability at TFG Brands (London)
Plan your priorities
The first step to mapping your multi-tier supply chain is to identify your key suppliers. These are the suppliers that have the biggest impact on your business, either in terms of volume, cost, or risk.
Retailers can gather this information from a variety of sources, including supplier lists from different departments, bills of materials, and supplier contracts.
If the retailer already has an ERP or PLM this can help but is not necessary.
Manage supplier resistance
Retailers need to support their suppliers initially. The Segura team can also engage with them to explain the benefits of the solution and how it can help strengthen their business relationship with you. For example, the solution helps suppliers identify potential risks, improve efficiency and reduce costs.
The most common causes for reduced engagement and supplier resistance are:- “We have no time for this” – We can quickly change this mindset by showing how quick and easy the software is to use and how it saves time overall.
- “We are experiencing delays” – Suppliers do have to gather information and make their own checks of their suppliers, which can take time. We recommend working with your suppliers to understand their needs and offer support for gathering and verifying data; we can also assist with this support.
- “We need time to learn the new system”- There is a learning curve with any new system, which is why we offer training sessions, have in-depth help files and ensure the system language can be selected by the user. Additionally, Segura has a dedicated support team that suppliers can contact for further assistance.
Tips to Minimise Resistance:
- Data format – Suppliers can upload information in any file format into Segura
- No language barriers – the Segura system is fully translated into native languages
- Regular supplier training and Q&A – Retailers who continue with an engagement programme as part of BAU have the greatest success with supply chain mapping and all the benefits that ensue.
Supply Chain Mapping Frequently Asked Questions
IS THERE MUCH SUPPLIER CROSS OVER BETWEEN DIFFERENT BRANDS?
We usually see around 30 - 40% cross-over, however, this percentage is increasing with each new client that joins our community.
HOW LONG DOES THE MAPPING PROCESS TAKE WITH SEGURA?
This depends on the number of suppliers you wish to onboard and the information that you’re looking to initially capture.
We recommend starting this process with a batch of around 50 suppliers. Include a mix of suppliers that you deem good and some you deem challenging, from an engagement perspective. This gives us a good data set to review. From the point of the first registration invite, it usually takes a few weeks to onboard and engage this initial group. We then work with you to evaluate the uptake, feedback and success, to help decide the best approach to onboard the rest.
Importantly, this as an ongoing project, suppliers will come and go, and the point of having active supply chain mapping is that you can see at any time who has supplied the business.
Make mapping your supply chain scalable, efficient and collaborative
In summary, supply chain mapping is best done using software like Segura's supply chain mapping tool, which is more scalable, efficient and collaborative than spreadsheets. then your teams can focus on what matters most. It makes mapping your supply chain, managing your supplier network, mitigating risk and driving improvements a seamless process.
Don’t make the job of mapping your supply chain more cumbersome and less rewarding than it ought to be. Plan properly, set realistic timelines, engage the right teams and use Segura for your supply chain mapping.
About Segura
Segura is the leading fashion supply chain traceability solution, empowering fashion retailers and brands to deliver ethical, sustainable and efficient multi-tier supply chains.
Segura provides n-tier mapping, transparency, traceability, visualisation, compliance and reporting. Segura sits in the centre of your supply chain management structure creating a central repository for all your supply chain, ESG-related data and evidence, including from third-party data sources.
With all supply chain traceability data stored on a single platform, our customers get the right evidence in the right place to back up claims and meet regulatory compliance.
To keep up to date with our latest news; subscribe to our newsletter
To learn more about how Segura can help you manage your supply chain; contact us today